The snow has long since melted, and we're now deep into Hokkaido's green season. That means snowboard building season for us.
As always, we start our production with the foundation: the wood core. This time around, we’d like to give you all a bit of insight into what makes our wood cores and what goes into them behind the scenes.
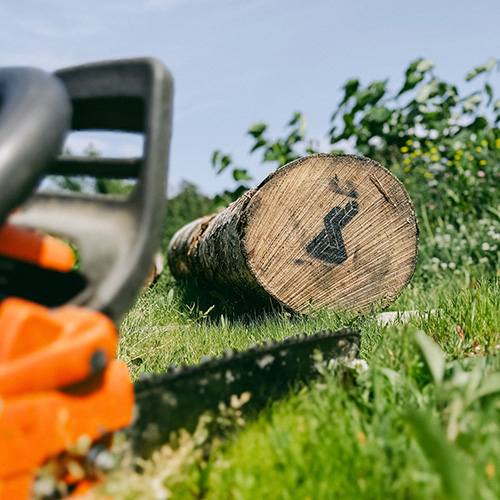
After extensive research, testing, and a bit of local advice from our timber supplier, we narrowed down our options to two indigenous species of wood that are both endemic to Hokkaido and Northeastern Asia. No need to import anything—all our timber is cut, seasoned, and prepared right here on the island. This means it stays in the same climate throughout its lifetime.
The bulk of the core is made up of honoki, or magnolia obovata. his species of tree has broad leaves and distinctive flowers, which are easy to spot throughout the Hokkaido landscape in the spring and summertime. You’ve probably already seen them and didn’t know it.
Historically, honoki has been used in Japan to carve bowls, spoons, and other household items. However, we found that after being cut and properly cured, honoki exhibits a lively flex and pop that translates perfectly to on-snow performance. Not to mention, it has an extremely light strength-to-weight ratio compared to more conventional woods used in snowboard manufacturing.
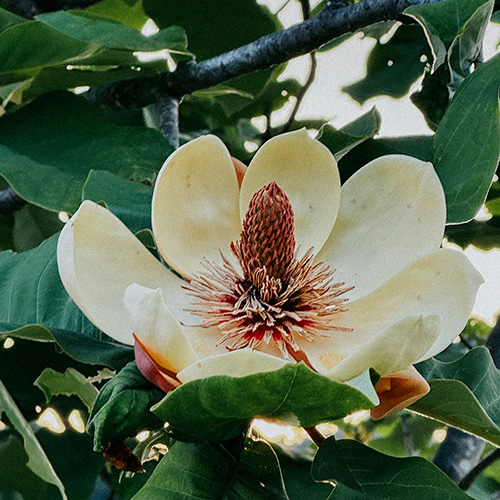
The other species of wood we use is called “tamo” or Manchurian Ash (Fraxinus mandshurica). This species is often used to craft musical instruments and furniture. Tamo has the perfect balance of flexural strength (how much it bends before breaking) and fiber density, making it a perfect central stringer material, adding strength and rigidity to our boards.
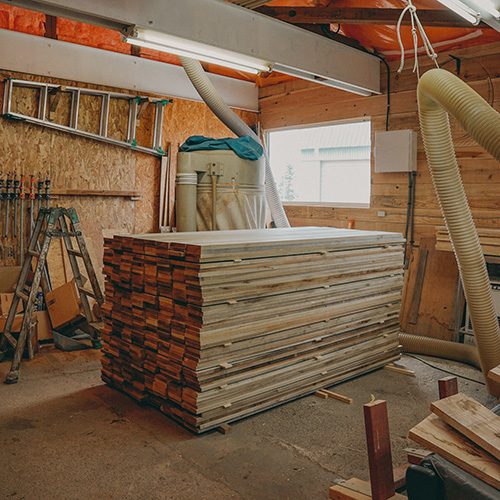
We hand-pick the lengths of each type of timber in the springtime. From there, we start the process by running every piece through the planer to ensure uniform thickness.
Each core block that we make is comprised of 15 separate lengths of timber, with one block yielding somewhere between 10-13 blank snowboard cores. That means a whole lot of time spent painstakingly feeding wood through a thickness planer by hand and inspecting them with a caliper for precision, but the end result makes it all worthwhile.
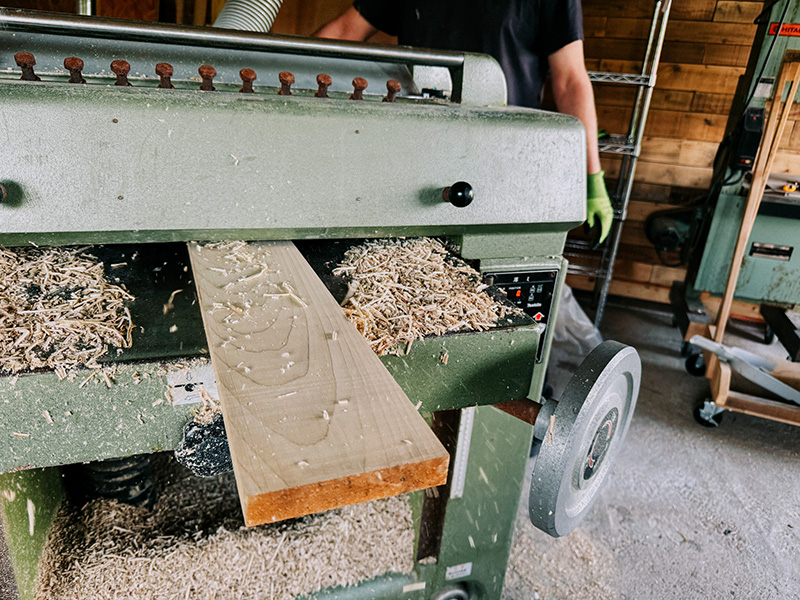

From there, it's a healthy coat of glue on each stringer. Then all the stringers are stacked and clamped together with even pressure to make solid core blocks. The blocks are then sliced into blank cores, ready to be shaped into our various designs.
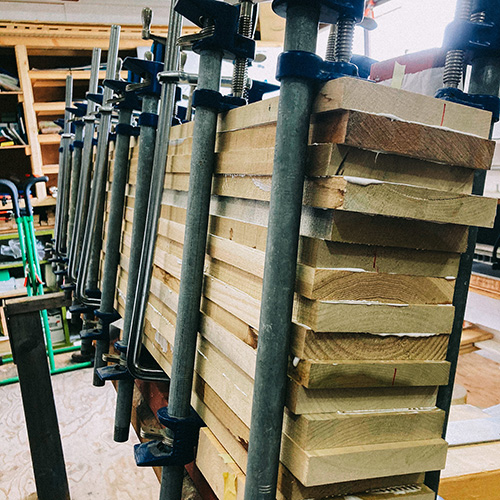
By separating our wood core construction process from other aspects of snowboard building, we can minimise wood waste contamination from plastics and other materials. This means our wood waste can go back to the local community as a usable resource and not just end up in a landfill. Some goes into local chicken coops, some into gardens and compost piles of friends and family, and some ends up as kindling to heat us through the cold Hokkaido winters. Everyone is constantly getting top-ups of sawdust, and what we don't send out the door gets used in our parking area and driveway throughout the year.
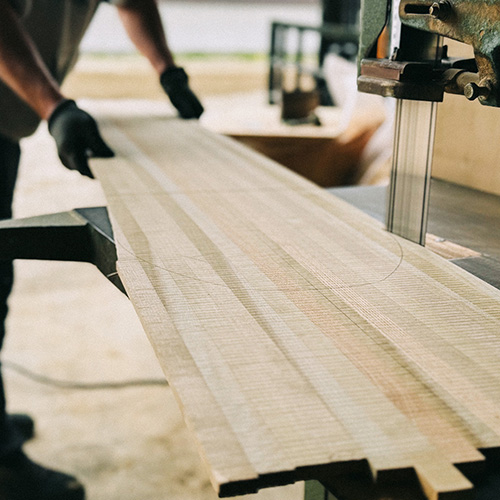
The wood core aspect of production is only a small part of the total snowboard building process. Honestly, what goes into taking the wood from loose planks to a finished core is just one piece of the puzzle, but we hope this gives you some insight into what it takes to produce the snowboards we call Island. We still find it incredible ourselves. Seeing how materials are used and why can bring a deeper appreciation for the work and time spent on each and every board.
If you're in the Niseko area or coming to town, drop by our workshop for a chat and a look into how our boards are built. You may even find yourself carrying one out under your arm.